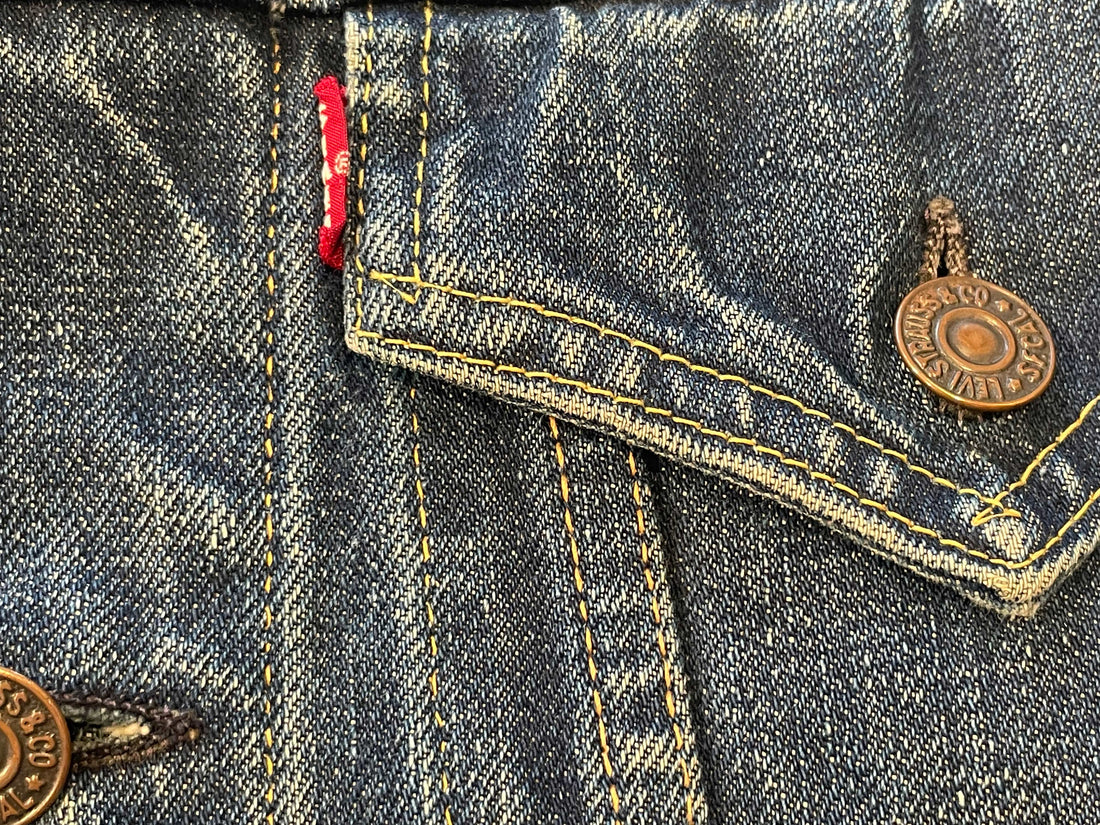
Vol.38 Denim
Share
The Olympics, which were fraught with problems right up until the last minute, have now begun, and Tokyo is starting to feel a bit like it's in an Olympic mood.
Since the atelier is close to the National Stadium, we could see the Blue Impulse beautifully.
But the traffic regulations are pretty strict.
Cars that normally use the highway came down to the streets, causing major road congestion, and people with local license plates coming to see the Olympic Stadium were behaving strangely, causing havoc in the Shibuya, Minato, and Chiyoda ward areas.
Everyone, please at least use your turn signals.
So, continuing from last time, I will continue writing about denim.
There doesn't seem to be anything particularly strange about it, but if you look closely at the stitching that holds the patch pocket in place, you'll see that the back is made with black #30 cotton thread.
However, the front looks like orange #20.
As I wrote last week, the threads used on the front and back are different.
Nowadays, processing has become commonplace, and instructions for sewing thread are written with the assumption that processing will be done.
In places where you want more puckering, use fewer stitches and use cotton thread on both the front and back.
In some places, the back thread is made thinner and the front thread is made thicker.
This is done intentionally and is possible with modern denim, but it seems strange to see this type of design on denim that is 70 years old.
One possibility is that products other than LEVI'S were also produced on the same line, and it was too much trouble to change the bobbin thread, so it remained black.
I read in a book that in addition to their own factories, they also use a number of affiliated factories, so could that have had an influence?
I think the yarn specifications are designed solely with production efficiency in mind.
I'm not sure if you can tell from the photo, but the decorative ST that appears on the basic front is based on orange.
However, the back is almost entirely yellow.
This is something that is commonplace and well known in modern times, but the grain (direction of the fabric) of the yoke is reversed.
The main body has a straight stitch, but the yoke has the reverse.
Considering the efficiency of the movement, I think it would be better to take it on the bias.
If the intention is to process the image, taking the picture with the grain normal will result in a flat appearance, so we reverse the grain in some places.
My guess is that since the back yoke is quite large, they made it upside down to save more fabric.
As a result, did the former York manager also experience adverse conditions?
In terms of saving fabric, this can be seen in the use of selvedge on the back of the front edge.
Selvedge is considered amazing nowadays, but this is just the edge of the fabric.
Because the fabric is woven on a power loom, it is possible to use the selvedge all the way up, but normally the selvedge part is not used as it is weak and may slip off.
Even if the fabric is 110cm wide (narrow width), the width excluding the selvedge is called the effective length.
I also think using the ears is a wise choice as it reduces the number of sewing processes as much as possible.
Normally it is finished by folding in thirds, or by finishing with a lock stitch and folding in half.
If you use the selvedge, you can finish the fabric by simply folding it in half, and it can be done with a straight stitch, which saves a lot of time.
Compared to making a shirt with all the seams folded, this is probably a lot easier to sew if you have a sewing machine and a trumpet.
If you're only making small items, you won't need to iron anything in the middle.
If I say too much, the factory might get angry.
I've also included a few photos of the 557XX.
This is also common to the 506XX and 507XX, but where the W stitch makes a sharp angle there is a stitch called a "watari" running through it.
It looks like the skipped thread you see in the center of Levi's arcuate stitching.
For this too, it takes time to run the edge ST (3mm) + 6mm to 7mm one by one, so we use a twin-needle sewing machine.
At sharp corners, the feed is increased once, resulting in a thigh gap on the inside.
It seems that it is possible to make it so that it doesn't appear these days, but when sewing denim, it looks better if the thigh crease is there.
In appearance, what makes it different from the 506XX and 507XX is that the tack buttons are copper colored.
It's a mystery why they chose copper, but...
It develops verdigris and transfers to other materials, so I think iron would have been better.
When I was in high school, the 70505 was available for under 10,000 yen, but I remember not buying it because I didn't like the copper color.
The biggest change has been the silhouette.
The 557XX has a body divided into nine panels to create a shaped waist.
In the 1950s, denim and white T-shirts became fashionable in films like "Robber" and "Rebel Without a Cause," and then became more popular, evolving from workwear to fashion, making this a memorable piece of clothing.
I used to dislike sardine sleeves, but now I feel like I can wear them without any discomfort.
It's the times.
Continuing from last time, I've been looking at jackets, but next time I cover denim I'd like to write about pants as well.
See you later!
NORI
48 comments
https://www.facebook.com/PrimeDropsForED.US/
https://www.facebook.com/groups/primedropsfored.us
https://www.facebook.com/groups/primedropsfored2025
https://www.facebook.com/events/2169340776895593/
https://www.facebook.com/events/2388695414883306/
https://whoherbsfree.zohodesk.com/portal/en/kb/articles/prime-drops-for-ed-is-it-safe-effective-read-it-before-buy
https://whoherbsfree.zohodesk.com/portal/en/kb/articles/prime-drops-for-ed-review-truth-must-read-before-buying
https://whoherbsfree.zohodesk.com/portal/en/kb/articles/prime-drops-for-ed-review-my-honest-opinion-and-results
https://whoherbsfree.zohodesk.com/portal/en/kb/articles/prime-drops-for-ed-happy-sex-life-is-it-worth-the-buzz
https://www.trysmallbiz.com/articles/prime-drops-for-ed-happy-sex-life-is-it-worth-the-buzz
https://www.trysmallbiz.com/articles/prime-drops-for-ed-is-it-safe-effective-read-it-before-buy
https://www.trysmallbiz.com/articles/prime-drops-for-ed-review-truth-must-read-before-buying
https://www.trysmallbiz.com/articles/prime-drops-for-ed-review-my-honest-opinion-and-results
https://primedropsed.alboompro.com/post/prime-drops-for-ed-happy-sex-life-is-it-worth-the-buzz
https://primedropsed.alboompro.com/post/prime-drops-for-ed-review-my-honest-opinion-and-results
https://primedropsed.alboompro.com/post/prime-drops-for-ed-review-truth-must-read-before-buying
https://primedropsed.alboompro.com/post/prime-drops-for-ed-is-it-safe-effective-read-it-before-buy
https://ollama.com/PrimeDropsForED
https://us.forum.dreametech.com/forum.php?mod=viewthread&tid=8102&extra=&post_redirect=1
https://eventprime.co/o/primedropsfored
https://www.facebook.com/EreforceGummiesusa/
https://www.facebook.com/groups/ereforcegummiesusa2025
https://www.facebook.com/events/1742038589785874/
https://www.facebook.com/groups/ereforcegummiesofficial2025
https://www.facebook.com/events/1085295473731697/
https://www.trysmallbiz.com/articles/ereforce-gummies-review-is-it-really-worth-the-hype
https://www.trysmallbiz.com/articles/ereforce-gummies-official-website-must-read-before-buy
https://www.trysmallbiz.com/articles/ereforce-gummies-review-truth-must-read-before-buying
https://www.trysmallbiz.com/articles/ereforce-gummies-natural-support-for-men-s-sexual-health-and-stamina
http://ereforcegummies.alboompro.com/portfolio/news/1551748-ereforce-gummies-expert-review-is-it-worth-your-money
https://ereforcegummies.alboompro.com/post/ereforce-gummies-can-it-really-improve-your-confidence
https://ereforcegummies.alboompro.com/post/ereforce-gummies-reviews-cost-scam-exposed
https://ereforcegummies.alboompro.com/post/ereforce-gummies-review-is-it-really-worth-the-hype
https://www.zupyak.com/p/4649707/t/ereforce-gummies-official-is-it-worth-the-hype
https://eventprime.co/o/EreforceGummiesusa
https://eventprime.co/o/EreforceGummiesusa2025
https://www.trustpilot.com/review/ereforcegummies.fesopoze.forexnews.bg
https://www.facebook.com/TrueAlphaGummiesUSA/
https://www.facebook.com/groups/truealphagummiesusa
https://www.facebook.com/groups/truealphagummies2025
https://www.facebook.com/events/769638852430165
https://www.facebook.com/events/1239888628345934/
https://www.trysmallbiz.com/articles/true-alpha-gummies-boost-stamina-confidence-wellness-naturally
https://www.trysmallbiz.com/articles/true-alpha-gummies-official-website-clinical-certified-100-natural
https://www.trysmallbiz.com/articles/true-alpha-gummies-review-is-it-really-worth-the-hype
https://www.trysmallbiz.com/articles/true-alpha-gummies-list-of-top-sex-pills-to-increase-sex-drive
https://www.zupyak.com/p/4649659/t/true-alpha-gummies-official-website-clinical-certified-100-natural
https://www.zupyak.com/p/4649662/t/true-alpha-gummies-list-of-top-sex-pills-to-increase-sex-drive
https://eventprime.co/o/TrueAlphaGummies
https://eventprime.co/o/TrueAlphaGummiesofficial
https://eventprime.co/o/TrueAlphaGummies2025
http://truealphagummies.alboompro.com/portfolio/news/1551743-true-alpha-gummies-official-website-clinical-certified-100-natural
http://truealphagummies.alboompro.com/portfolio/news/1551746-true-alpha-gummies-snake-oil-or-secret-weapon-let-s-talk
http://truealphagummies.alboompro.com/portfolio/news/1551747-true-alpha-gummies-review-is-it-really-worth-the-hype
https://truealphagummies.alboompro.com/post/true-alpha-gummies-for-sexual-health
https://truealphagummies.alboompro.com/post/true-alpha-gummies-is-it-worth-the-hype
https://truealphagummies.alboompro.com/post/true-alpha-gummies-official-website-clinical-certified-100-natural
https://whoherbsusa.zohodesk.in/portal/en/kb/articles/true-alpha-gummies-official-website-clinical-certified-100-natural
Ereforce Gummies: The Delicious Way to Support Your Wellness Journey
➢ (EXCLUSIVE OFFER) Click Here View the Pricing & Availability Ereforce Gummies
Adding essential nutrients to your daily routine can feel like a chore. Many people dread swallowing large pills or mixing gritty powders. This is where Scovia Gummies step in, offering a truly enjoyable and easy way to get vital nourishment.
https://www.facebook.com/EreforceGummiesusa/
https://www.facebook.com/groups/ereforcegummiesusa2025
https://www.facebook.com/events/1742038589785874/
https://www.facebook.com/groups/ereforcegummiesofficial2025
https://www.facebook.com/events/1085295473731697/
https://www.trysmallbiz.com/articles/ereforce-gummies-review-is-it-really-worth-the-hype
https://www.trysmallbiz.com/articles/ereforce-gummies-official-website-must-read-before-buy
https://www.trysmallbiz.com/articles/ereforce-gummies-review-truth-must-read-before-buying
https://www.trysmallbiz.com/articles/ereforce-gummies-natural-support-for-men-s-sexual-health-and-stamina
http://ereforcegummies.alboompro.com/portfolio/news/1551748-ereforce-gummies-expert-review-is-it-worth-your-money
https://ereforcegummies.alboompro.com/post/ereforce-gummies-can-it-really-improve-your-confidence
https://ereforcegummies.alboompro.com/post/ereforce-gummies-reviews-cost-scam-exposed
https://ereforcegummies.alboompro.com/post/ereforce-gummies-review-is-it-really-worth-the-hype
https://www.zupyak.com/p/4649707/t/ereforce-gummies-official-is-it-worth-the-hype
https://eventprime.co/o/EreforceGummiesusa
https://eventprime.co/o/EreforceGummiesusa2025
https://www.facebook.com/TrueAlphaGummiesUSA/
https://www.facebook.com/groups/truealphagummiesusa
https://www.facebook.com/groups/truealphagummies2025
https://www.facebook.com/events/769638852430165
https://www.facebook.com/events/1239888628345934/
https://www.trysmallbiz.com/articles/true-alpha-gummies-boost-stamina-confidence-wellness-naturally
https://www.trysmallbiz.com/articles/true-alpha-gummies-official-website-clinical-certified-100-natural
https://www.trysmallbiz.com/articles/true-alpha-gummies-review-is-it-really-worth-the-hype
https://www.trysmallbiz.com/articles/true-alpha-gummies-list-of-top-sex-pills-to-increase-sex-drive
https://www.zupyak.com/p/4649659/t/true-alpha-gummies-official-website-clinical-certified-100-natural
https://www.zupyak.com/p/4649662/t/true-alpha-gummies-list-of-top-sex-pills-to-increase-sex-drive
https://ereforcegummies.zohodesk.in/portal/en/kb/articles/ereforce-gummies-the-delicious-way-to-support-your-wellness-journey
https://eventprime.co/o/TrueAlphaGummies
https://eventprime.co/o/TrueAlphaGummiesofficial
https://eventprime.co/o/TrueAlphaGummies2025
http://truealphagummies.alboompro.com/portfolio/news/1551743-true-alpha-gummies-official-website-clinical-certified-100-natural
http://truealphagummies.alboompro.com/portfolio/news/1551746-true-alpha-gummies-snake-oil-or-secret-weapon-let-s-talk
http://truealphagummies.alboompro.com/portfolio/news/1551747-true-alpha-gummies-review-is-it-really-worth-the-hype
https://truealphagummies.alboompro.com/post/true-alpha-gummies-for-sexual-health
https://truealphagummies.alboompro.com/post/true-alpha-gummies-is-it-worth-the-hype
https://truealphagummies.alboompro.com/post/true-alpha-gummies-official-website-clinical-certified-100-natural
https://www.facebook.com/ScoviaGummies/
https://www.facebook.com/groups/scoviagummiesusa
https://www.facebook.com/events/773010711951584
https://www.facebook.com/groups/scoviagummiesnew
https://www.facebook.com/events/1987480755399407/
https://www.facebook.com/GreenStreetOriginsCBDGummiesUSA2025
https://www.facebook.com/groups/greenstreetoriginscbdgummiesnew
https://www.facebook.com/groups/greenstreetoriginscbdgummies.new2025
https://www.facebook.com/events/591573170553112/
https://www.facebook.com/events/1493550052089003/
https://primedropsed.alboompro.com/post/prime-drops-for-ed-happy-sex-life-is-it-worth-the-buzz
https://primedropsed.alboompro.com/post/prime-drops-for-ed-review-my-honest-opinion-and-results
https://primedropsed.alboompro.com/post/prime-drops-for-ed-review-truth-must-read-before-buying
https://primedropsed.alboompro.com/post/prime-drops-for-ed-is-it-safe-effective-read-it-before-buy
https://ollama.com/PrimeDropsForED
https://us.forum.dreametech.com/forum.php?mod=viewthread&tid=8102&extra=&post_redirect=1
https://whoherbsfree.zohodesk.com/portal/en/kb/articles/prime-drops-for-ed-is-it-safe-effective-read-it-before-buy
https://whoherbsfree.zohodesk.com/portal/en/kb/articles/prime-drops-for-ed-review-truth-must-read-before-buying
https://whoherbsfree.zohodesk.com/portal/en/kb/articles/prime-drops-for-ed-review-my-honest-opinion-and-results
https://whoherbsfree.zohodesk.com/portal/en/kb/articles/prime-drops-for-ed-happy-sex-life-is-it-worth-the-buzz
https://www.trysmallbiz.com/articles/prime-drops-for-ed-happy-sex-life-is-it-worth-the-buzz
https://www.trysmallbiz.com/articles/prime-drops-for-ed-is-it-safe-effective-read-it-before-buy
https://www.trysmallbiz.com/articles/prime-drops-for-ed-review-truth-must-read-before-buying
https://www.trysmallbiz.com/articles/prime-drops-for-ed-review-my-honest-opinion-and-results https://whoherbsfree.zohodesk.com/portal/en/kb/articles/scovia-gummies-official-website-must-read-before-buy
https://whoherbsfree.zohodesk.com/portal/en/kb/articles/scovia-gummies-natural-support-for-men-s-sexual-health-and-stamina
https://whoherbsusa.zohodesk.in/portal/en/kb/articles/true-alpha-gummies-official-website-clinical-certified-100-natural
Boost Your Vitality with True Alpha Gummies
➽➽(Official❤️Website)🧡
True Alpha Gummies support energy, stamina, and overall wellness. Packed with natural ingredients, they’re designed to enhance male performance and confidence. Feel stronger, energized, and focused daily.
https://www.facebook.com/TrueAlphaGummiesUSA/
https://www.facebook.com/groups/truealphagummiesusa
https://www.facebook.com/groups/truealphagummies2025
https://www.facebook.com/events/769638852430165
https://www.facebook.com/events/1239888628345934/
https://www.trysmallbiz.com/articles/true-alpha-gummies-boost-stamina-confidence-wellness-naturally
https://www.trysmallbiz.com/articles/true-alpha-gummies-official-website-clinical-certified-100-natural
https://www.trysmallbiz.com/articles/true-alpha-gummies-review-is-it-really-worth-the-hype
https://www.trysmallbiz.com/articles/true-alpha-gummies-list-of-top-sex-pills-to-increase-sex-drive
https://www.zupyak.com/p/4649659/t/true-alpha-gummies-official-website-clinical-certified-100-natural
https://www.zupyak.com/p/4649662/t/true-alpha-gummies-list-of-top-sex-pills-to-increase-sex-drive
https://eventprime.co/o/TrueAlphaGummies
https://eventprime.co/o/TrueAlphaGummiesofficial
https://eventprime.co/o/TrueAlphaGummies2025
http://truealphagummies.alboompro.com/portfolio/news/1551743-true-alpha-gummies-official-website-clinical-certified-100-natural
http://truealphagummies.alboompro.com/portfolio/news/1551746-true-alpha-gummies-snake-oil-or-secret-weapon-let-s-talk
http://truealphagummies.alboompro.com/portfolio/news/1551747-true-alpha-gummies-review-is-it-really-worth-the-hype
https://truealphagummies.alboompro.com/post/true-alpha-gummies-for-sexual-health
https://truealphagummies.alboompro.com/post/true-alpha-gummies-is-it-worth-the-hype
https://truealphagummies.alboompro.com/post/true-alpha-gummies-official-website-clinical-certified-100-natural
https://whoherbsusa.zohodesk.in/portal/en/kb/articles/true-alpha-gummies-review-is-it-really-worth-the-hype-20-8-2025
https://whoherbsusa.zohodesk.in/portal/en/kb/articles/true-alpha-gummies-official-website-clinical-certified-100-natural
https://www.facebook.com/EreforceGummiesusa/
https://www.facebook.com/groups/ereforcegummiesusa2025
https://www.facebook.com/events/1742038589785874/
https://www.facebook.com/groups/ereforcegummiesofficial2025
https://www.facebook.com/events/1085295473731697/
https://www.trysmallbiz.com/articles/ereforce-gummies-review-is-it-really-worth-the-hype
https://www.trysmallbiz.com/articles/ereforce-gummies-official-website-must-read-before-buy
https://www.trysmallbiz.com/articles/ereforce-gummies-review-truth-must-read-before-buying
https://www.trysmallbiz.com/articles/ereforce-gummies-natural-support-for-men-s-sexual-health-and-stamina
http://ereforcegummies.alboompro.com/portfolio/news/1551748-ereforce-gummies-expert-review-is-it-worth-your-money
https://ereforcegummies.alboompro.com/post/ereforce-gummies-can-it-really-improve-your-confidence
https://ereforcegummies.alboompro.com/post/ereforce-gummies-reviews-cost-scam-exposed
https://ereforcegummies.alboompro.com/post/ereforce-gummies-review-is-it-really-worth-the-hype
https://www.zupyak.com/p/4649707/t/ereforce-gummies-official-is-it-worth-the-hype
https://eventprime.co/o/EreforceGummiesusa
https://eventprime.co/o/EreforceGummiesusa2025
https://www.facebook.com/PrimeDropsForMenOfficial/
https://www.facebook.com/groups/primedropsformenofficial
https://www.facebook.com/groups/primedropsformennew
https://www.facebook.com/events/2254658221631010/
https://www.facebook.com/events/784211927518219/
https://www.facebook.com/Peak.Force.Pro.Male.Enhancement.Canada
https://www.facebook.com/groups/peak.force.pro.male.enhancement.canada
https://www.facebook.com/groups/peak.force.pro.male.enhancement.canada.2025
https://www.facebook.com/events/735167519332472/
https://www.facebook.com/events/741884045433025/
https://www.trysmallbiz.com/articles/peak-force-pro-male-enhancement-canada-review-is-it-really-worth-the-hype
https://www.trysmallbiz.com/articles/peak-force-pro-male-enhancement-canada-reviews-cost-scam-exposed
https://www.trysmallbiz.com/articles/peak-force-pro-male-enhancement-canada-official%E2%84%A2-is-it-worth-the-hype
https://www.trysmallbiz.com/articles/peak-force-pro-male-enhancement-canada-happy-sex-life-is-it-worth-the-buzz
https://www.zupyak.com/p/4647775/t/peak-force-pro-male-enhancement-canada-is-it-safe-and-effective-read-it-before-buy
https://www.zupyak.com/p/4647776/t/peak-force-pro-male-enhancement-canada-review-truth-must-read-before-buying
https://eventprime.co/o/peakforcepromaleenhancement
https://eventprime.co/o/PeakForceProMaleEnhancementCanada
https://community.3shape.com/forum/clinic-lab-collaboration-8/peak-force-pro-male-enhancement-canada-can-it-really-improve-your-confidence-1840
https://community.3shape.com/forum/clinic-lab-collaboration-8/peak-force-pro-male-enhancement-canada-review-is-it-really-worth-the-hype-1841
http://peakforceca.alboompro.com/portfolio/news/1548394-peak-force-pro-male-enhancement-canada-natural-support-for-stronger-erections-and-energy
http://peakforceca.alboompro.com/portfolio/news/1548404-peak-force-pro-male-enhancement-canada-benefits-and-experience
https://peakforceca.alboompro.com/portfolio/news/1548402-peak-force-pro-male-enhancement-canada-support-for-testosterone-stamina-size
https://www.facebook.com/ScoviaGummies/
https://www.facebook.com/groups/scoviagummiesusa
https://www.facebook.com/events/773010711951584
https://www.facebook.com/groups/scoviagummiesnew
https://www.facebook.com/events/1987480755399407/
https://www.facebook.com/Peak.Force.Pro.Male.Enhancement.Canada
https://www.facebook.com/groups/peak.force.pro.male.enhancement.canada
https://www.facebook.com/groups/peak.force.pro.male.enhancement.canada.2025
https://www.facebook.com/events/735167519332472/
https://www.facebook.com/events/741884045433025/
https://www.trysmallbiz.com/articles/peak-force-pro-male-enhancement-canada-review-is-it-really-worth-the-hype
https://www.trysmallbiz.com/articles/peak-force-pro-male-enhancement-canada-reviews-cost-scam-exposed
https://www.trysmallbiz.com/articles/peak-force-pro-male-enhancement-canada-official%E2%84%A2-is-it-worth-the-hype
https://www.trysmallbiz.com/articles/peak-force-pro-male-enhancement-canada-happy-sex-life-is-it-worth-the-buzz
https://www.zupyak.com/p/4647775/t/peak-force-pro-male-enhancement-canada-is-it-safe-and-effective-read-it-before-buy
https://www.zupyak.com/p/4647776/t/peak-force-pro-male-enhancement-canada-review-truth-must-read-before-buying
https://eventprime.co/o/peakforcepromaleenhancement
https://eventprime.co/o/PeakForceProMaleEnhancementCanada
http://peakforceca.alboompro.com/portfolio/news/1548394-peak-force-pro-male-enhancement-canada-natural-support-for-stronger-erections-and-energy
http://peakforceca.alboompro.com/portfolio/news/1548404-peak-force-pro-male-enhancement-canada-benefits-and-experience
https://peakforceca.alboompro.com/portfolio/news/1548402-peak-force-pro-male-enhancement-canada-support-for-testosterone-stamina-size
Prime Drops Male Enhancement Gummies: Boost Performance Naturally
🤑⋘🐱🚀⋘𝐒𝐩𝐞𝐜𝐢𝐚𝐥 𝐏𝐫𝐢𝐜𝐞❤️🌺𝗢𝐟𝐟𝐞𝐫 𝐂𝐡𝐞𝐜𝐤 𝐍𝐨𝐰⋙🐱🚀⋙🤑
Prime Drops Male Enhancement Gummies claim to support stamina, libido, and overall male performance using herbal ingredients. Designed for convenience, these gummies aim to enhance energy and confidence. While marketed as a natural supplement, users should consult a healthcare provider before use due to limited scientific backing.
https://www.facebook.com/GreenerFarmsCBDGummiesofficial.new
https://www.facebook.com/groups/greenerfarmscbdgummiesshop
https://www.facebook.com/groups/greenerfarmscbdgummiesbuy
https://www.facebook.com/events/1068579012123726/
https://www.facebook.com/events/1400743264319977/
https://eventprime.co/o/GreenerFarmsCBDGummiesnew
https://eventprime.co/o/GreenerFarmsCBDGummiesus
https://eventprime.co/o/GreenerFarmsCBDGummies2025
https://www.trysmallbiz.com/articles/greener-farms-cbd-gummies-truth-behind-the-claims
https://www.trysmallbiz.com/articles/greener-farms-cbd-gummies-does-it-work-or-not
https://www.trysmallbiz.com/articles/greener-farms-cbd-gummies-a-natural-path-to-wellness
https://www.trysmallbiz.com/articles/greener-farms-cbd-gummies-natural-support-for-mind-and-body
https://www.zupyak.com/p/4647194/t/greener-farms-cbd-gummies-truth-behind-the-claims
https://www.zupyak.com/p/4647196/t/greener-farms-cbd-gummies-does-it-work-or-not
https://www.zupyak.com/p/4647198/t/greener-farms-cbd-gummies-a-natural-path-to-wellness
https://www.zupyak.com/p/4647201/t/greener-farms-cbd-gummies-wellness-made-easy
https://community.3shape.com/forum/intraoral-scanning-and-software-5/greener-farms-cbd-gummiestruth-behind-the-claims-1704
https://community.3shape.com/forum/clinic-lab-collaboration-8/greener-farms-cbd-gummies-does-it-work-or-not-1705
https://www.trysmallbiz.com/articles/prime-drops-male-enhancement-gummies-review-truth-must-read-before-buying
https://www.trysmallbiz.com/articles/prime-drops-male-enhancement-gummies-fast-acting-formula-for-real-results
https://www.trysmallbiz.com/articles/prime-drops-male-enhancement-gummies-boost-your-vitality-naturally
https://www.trysmallbiz.com/articles/prime-drops-male-enhancement-gummies-natural-power-and-performance
https://www.facebook.com/ScoviaMaleEnhancementOfficial
https://www.facebook.com/groups/scoviamaleenhancementofficial
https://www.facebook.com/groups/scoviamaleenhancement2025
https://www.facebook.com/events/3246029312221723/
https://www.facebook.com/events/788413223590991/
https://dipefo.alboompro.com/portfolio/health/1546476-prime-drops-male-enhancement-gummies-fast-acting-formula-for-real-results
http://dipefo.alboompro.com/portfolio/news/1546482-prime-drops-male-enhancement-gummies-natural-power-and-performance
http://dipefo.alboompro.com/portfolio/news/1546584-prime-drops-male-enhancement-gummies-review-truth-must-read-before-buying
http://dipefo.alboompro.com/portfolio/news/1546585-prime-drops-male-enhancement-gummies-our-daily-path-to-calm
https://eventprime.co/o/PrimeDropsMaleEnhancementGummies
https://eventprime.co/o/PrimeDropsMaleEnhancementGummiesNew
https://www.facebook.com/GreenStreetOriginsCBDGummiesUSA2025
https://www.facebook.com/groups/greenstreetoriginscbdgummiesnew
https://www.facebook.com/groups/greenstreetoriginscbdgummies.new2025
https://www.facebook.com/events/591573170553112/
https://www.facebook.com/events/1493550052089003/
https://www.trysmallbiz.com/articles/golden-fountain-farms-cbd-gummies-what%E2%80%99s-inside-and-how-it-works
https://www.trysmallbiz.com/articles/golden-fountain-farms-cbd-gummies-official-website-must-read-before-buy-5280
https://www.trysmallbiz.com/articles/golden-fountain-farms-cbd-gummies-natural-support-for-men-s-sexual-health-and-stamina
https://www.trysmallbiz.com/articles/golden-fountain-farms-cbd-gummies-review-truth-must-read-before-buying-5278
http://greenstreetorigins8.alboompro.com/portfolio/news/1546909-green-street-origins-cbd-gummies-is-it-safe-effective-read-it-before-buy
http://greenstreetorigins8.alboompro.com/portfolio/news/1546980-golden-fountain-farms-cbd-gummies-review-my-honest-opinion-and-results
http://greenstreetorigins8.alboompro.com/portfolio/news/1546982-green-street-origins-cbd-gummies-review-is-it-really-worth-the-hype
http://greenstreetorigins8.alboompro.com/portfolio/news/1546983-golden-fountain-farms-cbd-gummies-official-website-must-read-before-buy
https://eventprime.co/o/GreenStreetOriginsCBDGummiesusa
https://eventprime.co/o/GreenStreetOriginsCBDGummiesnew
https://sites.google.com/view/goldenfountainfarmscbdgummieso/
https://www.zupyak.com/p/4647193/t/green-street-origins-cbd-gummies-review-is-it-really-worth-the-hype
https://www.zupyak.com/p/4647197/t/golden-fountain-farms-cbd-gummies-official-website-must-read-before-buy
https://www.zupyak.com/p/4647199/t/golden-fountain-farms-cbd-gummies-review-truth-must-read-before-buying
https://www.zupyak.com/p/4647202/t/golden-fountain-farms-cbd-gummies-natural-support-for-mens-sexual-health-and-stamina
https://community.3shape.com/forum/intraoral-scanning-and-software-5/-green-street-origins-cbd-gummies-is-it-safe-effective-read-it-before-buy-1706
https://community.3shape.com/forum/clinic-lab-collaboration-8/green-street-origins-cbd-gummies-review-is-it-really-worth-the-hype-1707
https://www.facebook.com/GreenerFarmsCBDGummiesofficial.new
https://www.facebook.com/groups/greenerfarmscbdgummiesshop
https://www.facebook.com/groups/greenerfarmscbdgummiesbuy
https://www.facebook.com/events/1068579012123726/
https://www.facebook.com/events/1400743264319977/
https://eventprime.co/o/GreenerFarmsCBDGummiesnew
https://eventprime.co/o/GreenerFarmsCBDGummiesus
https://eventprime.co/o/GreenerFarmsCBDGummies2025
https://www.trysmallbiz.com/articles/greener-farms-cbd-gummies-truth-behind-the-claims
https://www.trysmallbiz.com/articles/greener-farms-cbd-gummies-does-it-work-or-not
https://www.trysmallbiz.com/articles/greener-farms-cbd-gummies-a-natural-path-to-wellness
https://www.trysmallbiz.com/articles/greener-farms-cbd-gummies-natural-support-for-mind-and-body
https://www.zupyak.com/p/4647194/t/greener-farms-cbd-gummies-truth-behind-the-claims
https://www.zupyak.com/p/4647196/t/greener-farms-cbd-gummies-does-it-work-or-not
https://www.zupyak.com/p/4647198/t/greener-farms-cbd-gummies-a-natural-path-to-wellness
https://www.zupyak.com/p/4647201/t/greener-farms-cbd-gummies-wellness-made-easy
https://community.3shape.com/forum/intraoral-scanning-and-software-5/greener-farms-cbd-gummiestruth-behind-the-claims-1704
https://community.3shape.com/forum/clinic-lab-collaboration-8/greener-farms-cbd-gummies-does-it-work-or-not-1705
https://www.facebook.com/ScionOrganicsCBDGummiesNew/
https://www.facebook.com/groups/scionorganicscbdgummiesnew
https://www.facebook.com/groups/scionorganicscbdgummiesus2025
https://www.facebook.com/events/2155920224918428/
https://www.facebook.com/events/1279655703062179/