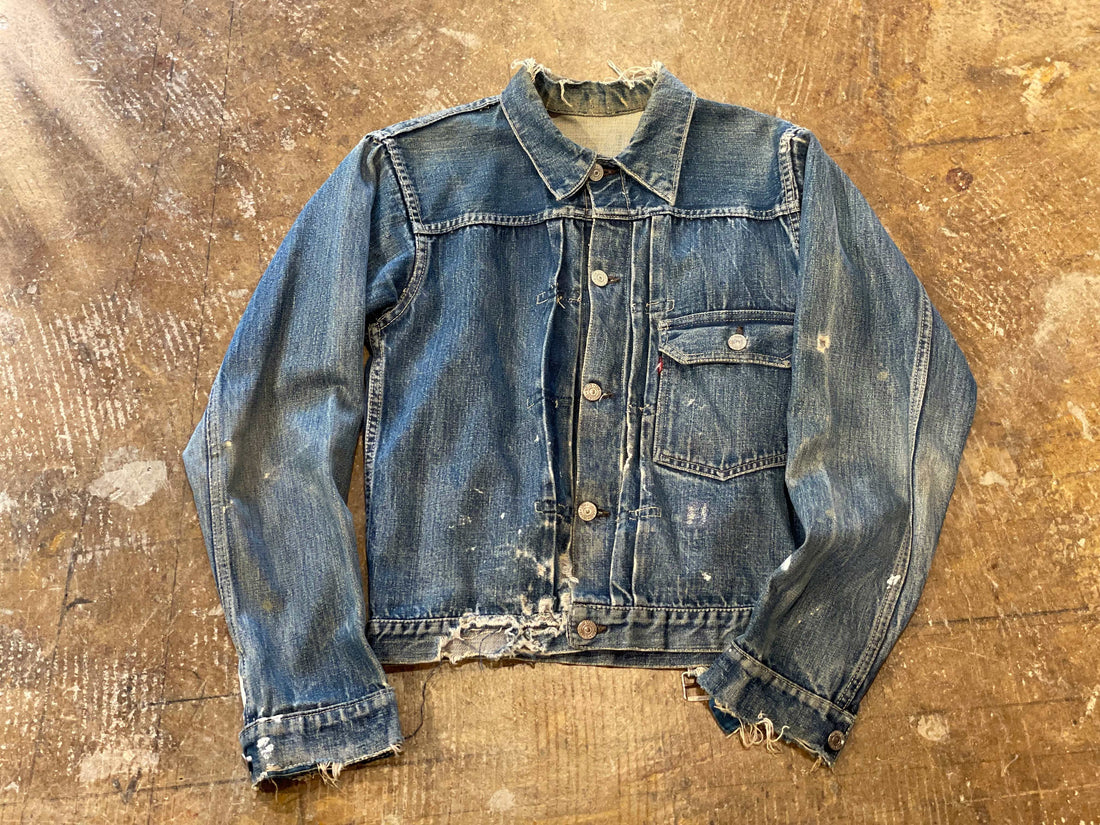
Vol.37 It's the climax
Share
The rainy season is now gradually coming to an end in Japan.
The dreaded rainy season ended in the blink of an eye.
From here on, it's scorching hot hell on the bike.
Everyone please be careful not to get heatstroke.
This year, we have been busy with the Olympics, so we are working hard to create samples.
The pattern maker is not showing his true potential, so I'm quite worried about whether it will go through.
So this time I'd like to write about things related to the denim jackets I always make.
With the recent vintage boom, prices of Levi's have been skyrocketing, but I used to hunt for them a lot when I was younger, so I can buy them at cheaper prices than I do now.
We have a kind of blueprint called a thread instruction sheet that we send to the factory, but for a normal riders jacket, the thread instructions are simply something like "matching the outer fabric color, #20 (thread number), number of stitches, polyester filament" to match the leather.
However, denim is so complicated that it has to be drawn out on an unfolded diagram.
Why is denim so complicated?
First, you can choose between cotton and polyester thread depending on the era you want to make it.
If strength is required, core yarn (polyester yarn wrapped with cotton) can be used.
In some cases, the upper thread is core and the lower thread is poly.
The combination is decided based on experience and predictions about what state we want the finished product to be in after processing, and what it will look like after 10 years of wear.
I've blurred it because it's a trade secret, but the general idea is something like this.
Basically, it specifies all the threads.
I don't think a normal factory would do this.
I needed vintage denim to create these instructions, so I went on a shopping spree.
If I'm going to buy things, I want them to be something I can wear, so they're all in my size.
When adding processing, realistic processing does not come about solely through the skill of the craftsman.
It depends on how far you want to go, but if you are pursuing a vintage feel, you need to know everything about vintage items to create something that satisfies you.
So, I'm just about to write the thread instructions, so I'll post some pictures of the vintage threads and their specifications.
First, the 1st (506XX)
Originally, the name XX was chosen to denote a sturdy fabric, the thickest available with the technology available at the time.
This is well known, but the back of the flap is made of thin denim of about 6oz.
It looks like it's been thinned to reduce the thickness.
I've always wondered, why did they insist on making it thin even though they could roll the kama bottom?
I wonder if it wouldn't have fit if I used a straight sewing machine?
Rivets are used at the opening of the patch pocket.
It must be a remnant of the S506XX.
By the way, these days I finish the opening with a triple fold, but the 557XX is left raw.
The age can be determined by the cinch back, but the age can also be determined by the rivets.
This is the earlier 506XX
This is what is used later.
Can you see the difference?
The stamps on the early period are closer to the inside and the letters are small, but the stamps on the later period are larger.
The larger letters are also used for 507XX.
If the cinch back is broken you can tell the age by looking here.
By the way, the cinch back of the previous model looks like this.
Items with two needles are from the early period.
We can't make them now because we have to think about the consumer and hedge our risks.
There are similar items, but the basic needles cannot be used.
Look at the sewing specifications.
This is the biggest difference between the sewing specifications of 506XX and 507XX.
The 506XX does not use a trumpet to attach the cuffs.
It's more like attaching shirt cuffs.
So the chain st is not running.
On the other hand, the 507XX uses a trumpet.
Since it is made of a trumpet, the back is made of a chain.
A trumpet is an attachment that is attached to a sewing machine, and roughly speaking it is a time-saving device when sewing.
If you're interested, please Google it.
Just looking at this, you can see the shift in the times from tailoring to mass production.
Looking at the threads used on the front, you can see that a variety of thread counts have been used, but what's interesting is the back.
It consists of a chain of basic wrap stitches.
This is thought to be for strength against tension.
However, if part of the chain breaks, the thread will fray in one direction from that point.
Since it was used as workwear in the past, I think this was a simple measure that prioritized sewing efficiency over durability.
Using a trumpet stitch is much more efficient and saves time than sewing everything with folded hem.
If you undo the rolled stitching you will see that the seam allowances are also cut very roughly.
I'm not sure why this is, but sometimes the colors of the upper thread and bobbin thread are slightly different.
This is the back of a two-piece sleeve, but can you see that the top and bottom are different colors?
The top is orange and the bottom is yellow.
I think it's a hassle to change the color just by doing that, but I often see colors changed like this.
This is not limited to the 506XX, but continues into the 557XX era.
The 506XX was released around the late 1930s, and the 557XX in the 1960s.
It has been sewn in the same way for about 30 years.
. . . This is getting quite long, so I'll write about 507XX and 557XX next time.
As a craftsman, I feel a greater attachment to pieces that are made over a long period of time, with detailed instructions even down to the thread used.
Although more than 70% of it is for my own satisfaction, I will do my best to create a product that can be talked about in many ways.
On a different note, we have some new Ezo bear wallets in stock today, so please come by the store and feel free to touch them.
I'm not sure whether to put it on the online shop.
See you later!
NORI
14 comments
https://www.facebook.com/Peak.Force.Pro.Male.Enhancement.Canada
https://www.facebook.com/groups/peak.force.pro.male.enhancement.canada
https://www.facebook.com/groups/peak.force.pro.male.enhancement.canada.2025
https://www.facebook.com/events/735167519332472/
https://www.facebook.com/events/741884045433025/
https://www.trysmallbiz.com/articles/peak-force-pro-male-enhancement-canada-review-is-it-really-worth-the-hype
https://www.trysmallbiz.com/articles/peak-force-pro-male-enhancement-canada-reviews-cost-scam-exposed
https://www.trysmallbiz.com/articles/peak-force-pro-male-enhancement-canada-official%E2%84%A2-is-it-worth-the-hype
https://www.trysmallbiz.com/articles/peak-force-pro-male-enhancement-canada-happy-sex-life-is-it-worth-the-buzz
https://www.zupyak.com/p/4647775/t/peak-force-pro-male-enhancement-canada-is-it-safe-and-effective-read-it-before-buy
https://www.zupyak.com/p/4647776/t/peak-force-pro-male-enhancement-canada-review-truth-must-read-before-buying
https://eventprime.co/o/peakforcepromaleenhancement
https://eventprime.co/o/PeakForceProMaleEnhancementCanada
http://peakforceca.alboompro.com/portfolio/news/1548394-peak-force-pro-male-enhancement-canada-natural-support-for-stronger-erections-and-energy
http://peakforceca.alboompro.com/portfolio/news/1548404-peak-force-pro-male-enhancement-canada-benefits-and-experience
https://peakforceca.alboompro.com/portfolio/news/1548402-peak-force-pro-male-enhancement-canada-support-for-testosterone-stamina-size
Prime Drops Male Enhancement Gummies: Boost Performance Naturally
🤑⋘🐱🚀⋘𝐒𝐩𝐞𝐜𝐢𝐚𝐥 𝐏𝐫𝐢𝐜𝐞❤️🌺𝗢𝐟𝐟𝐞𝐫 𝐂𝐡𝐞𝐜𝐤 𝐍𝐨𝐰⋙🐱🚀⋙🤑
Prime Drops Male Enhancement Gummies claim to support stamina, libido, and overall male performance using herbal ingredients. Designed for convenience, these gummies aim to enhance energy and confidence. While marketed as a natural supplement, users should consult a healthcare provider before use due to limited scientific backing.
https://www.facebook.com/GreenerFarmsCBDGummiesofficial.new
https://www.facebook.com/groups/greenerfarmscbdgummiesshop
https://www.facebook.com/groups/greenerfarmscbdgummiesbuy
https://www.facebook.com/events/1068579012123726/
https://www.facebook.com/events/1400743264319977/
https://eventprime.co/o/GreenerFarmsCBDGummiesnew
https://eventprime.co/o/GreenerFarmsCBDGummiesus
https://eventprime.co/o/GreenerFarmsCBDGummies2025
https://www.trysmallbiz.com/articles/greener-farms-cbd-gummies-truth-behind-the-claims
https://www.trysmallbiz.com/articles/greener-farms-cbd-gummies-does-it-work-or-not
https://www.trysmallbiz.com/articles/greener-farms-cbd-gummies-a-natural-path-to-wellness
https://www.trysmallbiz.com/articles/greener-farms-cbd-gummies-natural-support-for-mind-and-body
https://www.zupyak.com/p/4647194/t/greener-farms-cbd-gummies-truth-behind-the-claims
https://www.zupyak.com/p/4647196/t/greener-farms-cbd-gummies-does-it-work-or-not
https://www.zupyak.com/p/4647198/t/greener-farms-cbd-gummies-a-natural-path-to-wellness
https://www.zupyak.com/p/4647201/t/greener-farms-cbd-gummies-wellness-made-easy
https://community.3shape.com/forum/intraoral-scanning-and-software-5/greener-farms-cbd-gummiestruth-behind-the-claims-1704
https://community.3shape.com/forum/clinic-lab-collaboration-8/greener-farms-cbd-gummies-does-it-work-or-not-1705
https://www.trysmallbiz.com/articles/prime-drops-male-enhancement-gummies-review-truth-must-read-before-buying
https://www.trysmallbiz.com/articles/prime-drops-male-enhancement-gummies-fast-acting-formula-for-real-results
https://www.trysmallbiz.com/articles/prime-drops-male-enhancement-gummies-boost-your-vitality-naturally
https://www.trysmallbiz.com/articles/prime-drops-male-enhancement-gummies-natural-power-and-performance
https://www.facebook.com/ScoviaMaleEnhancementOfficial
https://www.facebook.com/groups/scoviamaleenhancementofficial
https://www.facebook.com/groups/scoviamaleenhancement2025
https://www.facebook.com/events/3246029312221723/
https://www.facebook.com/events/788413223590991/
https://dipefo.alboompro.com/portfolio/health/1546476-prime-drops-male-enhancement-gummies-fast-acting-formula-for-real-results
http://dipefo.alboompro.com/portfolio/news/1546482-prime-drops-male-enhancement-gummies-natural-power-and-performance
http://dipefo.alboompro.com/portfolio/news/1546584-prime-drops-male-enhancement-gummies-review-truth-must-read-before-buying
http://dipefo.alboompro.com/portfolio/news/1546585-prime-drops-male-enhancement-gummies-our-daily-path-to-calm
https://eventprime.co/o/PrimeDropsMaleEnhancementGummies
https://eventprime.co/o/PrimeDropsMaleEnhancementGummiesNew
https://www.facebook.com/GreenStreetOriginsCBDGummiesUSA2025
https://www.facebook.com/groups/greenstreetoriginscbdgummiesnew
https://www.facebook.com/groups/greenstreetoriginscbdgummies.new2025
https://www.facebook.com/events/591573170553112/
https://www.facebook.com/events/1493550052089003/
https://www.trysmallbiz.com/articles/golden-fountain-farms-cbd-gummies-what%E2%80%99s-inside-and-how-it-works
https://www.trysmallbiz.com/articles/golden-fountain-farms-cbd-gummies-official-website-must-read-before-buy-5280
https://www.trysmallbiz.com/articles/golden-fountain-farms-cbd-gummies-natural-support-for-men-s-sexual-health-and-stamina
https://www.trysmallbiz.com/articles/golden-fountain-farms-cbd-gummies-review-truth-must-read-before-buying-5278
http://greenstreetorigins8.alboompro.com/portfolio/news/1546909-green-street-origins-cbd-gummies-is-it-safe-effective-read-it-before-buy
http://greenstreetorigins8.alboompro.com/portfolio/news/1546980-golden-fountain-farms-cbd-gummies-review-my-honest-opinion-and-results
http://greenstreetorigins8.alboompro.com/portfolio/news/1546982-green-street-origins-cbd-gummies-review-is-it-really-worth-the-hype
http://greenstreetorigins8.alboompro.com/portfolio/news/1546983-golden-fountain-farms-cbd-gummies-official-website-must-read-before-buy
https://eventprime.co/o/GreenStreetOriginsCBDGummiesusa
https://eventprime.co/o/GreenStreetOriginsCBDGummiesnew
https://sites.google.com/view/goldenfountainfarmscbdgummieso/
https://www.zupyak.com/p/4647193/t/green-street-origins-cbd-gummies-review-is-it-really-worth-the-hype
https://www.zupyak.com/p/4647197/t/golden-fountain-farms-cbd-gummies-official-website-must-read-before-buy
https://www.zupyak.com/p/4647199/t/golden-fountain-farms-cbd-gummies-review-truth-must-read-before-buying
https://www.zupyak.com/p/4647202/t/golden-fountain-farms-cbd-gummies-natural-support-for-mens-sexual-health-and-stamina
https://community.3shape.com/forum/intraoral-scanning-and-software-5/-green-street-origins-cbd-gummies-is-it-safe-effective-read-it-before-buy-1706
https://community.3shape.com/forum/clinic-lab-collaboration-8/green-street-origins-cbd-gummies-review-is-it-really-worth-the-hype-1707
https://www.facebook.com/GreenerFarmsCBDGummiesofficial.new
https://www.facebook.com/groups/greenerfarmscbdgummiesshop
https://www.facebook.com/groups/greenerfarmscbdgummiesbuy
https://www.facebook.com/events/1068579012123726/
https://www.facebook.com/events/1400743264319977/
https://eventprime.co/o/GreenerFarmsCBDGummiesnew
https://eventprime.co/o/GreenerFarmsCBDGummiesus
https://eventprime.co/o/GreenerFarmsCBDGummies2025
https://www.trysmallbiz.com/articles/greener-farms-cbd-gummies-truth-behind-the-claims
https://www.trysmallbiz.com/articles/greener-farms-cbd-gummies-does-it-work-or-not
https://www.trysmallbiz.com/articles/greener-farms-cbd-gummies-a-natural-path-to-wellness
https://www.trysmallbiz.com/articles/greener-farms-cbd-gummies-natural-support-for-mind-and-body
https://www.zupyak.com/p/4647194/t/greener-farms-cbd-gummies-truth-behind-the-claims
https://www.zupyak.com/p/4647196/t/greener-farms-cbd-gummies-does-it-work-or-not
https://www.zupyak.com/p/4647198/t/greener-farms-cbd-gummies-a-natural-path-to-wellness
https://www.zupyak.com/p/4647201/t/greener-farms-cbd-gummies-wellness-made-easy
https://community.3shape.com/forum/intraoral-scanning-and-software-5/greener-farms-cbd-gummiestruth-behind-the-claims-1704
https://community.3shape.com/forum/clinic-lab-collaboration-8/greener-farms-cbd-gummies-does-it-work-or-not-1705
https://www.facebook.com/ScionOrganicsCBDGummiesNew/
https://www.facebook.com/groups/scionorganicscbdgummiesnew
https://www.facebook.com/groups/scionorganicscbdgummiesus2025
https://www.facebook.com/events/2155920224918428/
https://www.facebook.com/events/1279655703062179/
Scovia Male Enhancement: Boost Your Performance Naturally
Scovia Male Enhancement is a powerful supplement designed to support male vitality, stamina, and performance. Formulated with natural ingredients, it helps improve blood circulation, boost testosterone levels, and enhance energy and endurance. Men using Scovia often report increased confidence, better physical performance, and improved libido. The formula works by stimulating the body’s natural processes, making it a safe and effective option for those seeking enhanced results without harmful side effects. Whether you’re looking to reignite passion or simply feel more energized, Scovia Male Enhancement offers a reliable, natural solution to support a healthier, more active lifestyle.
https://www.facebook.com/ScoviaMaleEnhancementOfficial
https://www.facebook.com/groups/scoviamaleenhancementofficial
https://www.facebook.com/groups/scoviamaleenhancement2025
https://www.facebook.com/events/3246029312221723/
https://www.facebook.com/events/788413223590991/
https://www.trysmallbiz.com/articles/scovia-male-enhancement-review-is-it-really-worth-the-hype
https://www.trysmallbiz.com/articles/scovia-male-enhancement-list-of-top-sex-pills-to-increase-sex-drive
https://www.trysmallbiz.com/articles/scovia-male-enhancement-is-it-worth-the-hype
https://www.trysmallbiz.com/articles/scovia-male-enhancement-your-daily-path-to-calm
https://medium.com/heath.jacky/scovia-male-enhancement-for-sexual-health-79889d97d640 https://medium.com/heath.jacky/scovia-male-enhancement-review-is-it-really-worth-the-hype-bbeeeb63dba4
https://medium.com/heath.jacky/scovia-male-enhancement-is-it-worth-the-hype-c2c6479938b6 https://www.zupyak.com/p/4646330/t/scovia-male-enhancement-for-sexual-health https://www.zupyak.com/p/4646335/t/scovia-male-enhancement-review-is-it-really-worth-the-hype https://www.zupyak.com/p/4646336/t/scovia-male-enhancement-list-of-top-sex-pills-to-increase-sex-drive https://www.zupyak.com/p/4646346/t/scovia-male-enhancement-your-daily-path-to-calm https://eventprime.co/o/ScoviaMaleEnhancementOfficial https://eventprime.co/o/ScoviaMaleEnhancementNew https://eventprime.co/o/ScoviaMaleEnhancement2025 https://www.facebook.com/ScionOrganicsCBDGummiesNew/ https://www.facebook.com/groups/scionorganicscbdgummiesnew https://www.facebook.com/groups/scionorganicscbdgummiesus2025 https://www.facebook.com/events/2155920224918428/ https://www.facebook.com/events/1279655703062179/ https://www.facebook.com/SerenityVowCBDGummiesUSA/ https://www.facebook.com/groups/serenityvowcbdgummies2025 https://www.facebook.com/groups/serenityvowcbdgummiesusa https://www.facebook.com/events/767600409086247/ https://www.facebook.com/events/1495170468074781/ https://nas.io/root-labs-alpha-gummies-3/challenges/oxvia-male-enhancement-gummies-review-truth-must-read-before-buying https://nas.io/root-labs-alpha-gummies-3/challenges/oxvia-male-enhancement-gummies-review-is-it-really-worth-the-hype https://www.zupyak.com/p/4646118/t/oxvia-male-enhancement-gummies-review-is-it-really-worth-the-hype https://www.zupyak.com/p/4646119/t/oxvia-male-enhancement-gummies-review-truth-must-read-before-buying https://www.zupyak.com/p/4646120/t/oxvia-male-enhancement-gummies-my-honest-reviews-does-it-really-work-or-is-it-just-hype https://www.zupyak.com/p/4646121/t/oxvia-male-enhancement-gummies-is-it-safe-read-experts-opinion https://whoherbs.com/oxvia-male-enhancement-gummies/ https://www.facebook.com/GoldenFountainFarmsCBDGummiesusa/ https://www.facebook.com/groups/goldenfountainfarmscbdgummies.new https://www.facebook.com/groups/goldenfountainfarmscbdgummies.us2025 https://www.facebook.com/events/1874958893425777 https://www.facebook.com/events/1769232153982095 https://www.trysmallbiz.com/articles/golden-fountain-farms-cbd-gummies-is-it-safe-effective-read-it-before-buy https://www.trysmallbiz.com/articles/golden-fountain-farms-cbd-gummies-official-website-must-read-before-buy https://www.trysmallbiz.com/articles/golden-fountain-farms-cbd-gummies-review-truth-must-read-before-buying https://www.trysmallbiz.com/articles/golden-fountain-farms-cbd-gummies-is-it-safe-read-experts-opinion https://sites.google.com/view/goldenfountainfarmscbdgummiesi/home http://goldenfountain3.alboompro.com/portfolio/news/1545435-golden-fountain-farms-cbd-gummies-review-is-it-really-worth-the-hype http://goldenfountain3.alboompro.com/portfolio/news/1545436-golden-fountain-farms-cbd-gummies-official-website-must-read-before-buy http://goldenfountain3.alboompro.com/portfolio/news/1545437-golden-fountain-farms-cbd-gummies-a-breakthrough-for-male-performance-stamina http://goldenfountain3.alboompro.com/portfolio/news/1545439-golden-fountain-farms-cbd-gummies-is-it-safe-read-experts-opinion https://eventprime.co/o/GoldenFountainFarmsCBDGummiesus https://eventprime.co/o/GoldenFountainFarmsCBDGummiesusa https://www.zupyak.com/p/4646394/t/golden-fountain-farms-cbd-gummies-review-my-honest-opinion-and-results https://www.zupyak.com/p/4646401/t/golden-fountain-farms-cbd-gummies-is-it-safe-read-experts-opinion https://www.zupyak.com/p/4646411/t/golden-fountain-farms-cbd-gummies-review-truth-must-read-before-buying https://www.zupyak.com/p/4646413/t/golden-fountain-farms-cbd-gummies-whats-inside-and-how-it-works https://medium.com/hidyloxi/golden-fountain-farms-cbd-gummies-official-website-must-read-before-buy-f4189ba2b056
https://medium.com/hidyloxi/golden-fountain-farms-cbd-gummies-is-it-safe-read-experts-opinion-f3c39a3c0b55 https://www.facebook.com/GoldenFountainFarmsCBDGummiesusa/ https://www.facebook.com/groups/goldenfountainfarmscbdgummies.new https://www.facebook.com/groups/goldenfountainfarmscbdgummies.us2025 https://www.facebook.com/events/1874958893425777 https://www.facebook.com/events/1769232153982095 https://www.trysmallbiz.com/articles/golden-fountain-farms-cbd-gummies-is-it-safe-effective-read-it-before-buy https://www.trysmallbiz.com/articles/golden-fountain-farms-cbd-gummies-official-website-must-read-before-buy https://www.trysmallbiz.com/articles/golden-fountain-farms-cbd-gummies-review-truth-must-read-before-buying https://www.trysmallbiz.com/articles/golden-fountain-farms-cbd-gummies-is-it-safe-read-experts-opinion https://sites.google.com/view/goldenfountainfarmscbdgummiesi/home http://goldenfountain3.alboompro.com/portfolio/news/1545435-golden-fountain-farms-cbd-gummies-review-is-it-really-worth-the-hype http://goldenfountain3.alboompro.com/portfolio/news/1545436-golden-fountain-farms-cbd-gummies-official-website-must-read-before-buy http://goldenfountain3.alboompro.com/portfolio/news/1545437-golden-fountain-farms-cbd-gummies-a-breakthrough-for-male-performance-stamina http://goldenfountain3.alboompro.com/portfolio/news/1545439-golden-fountain-farms-cbd-gummies-is-it-safe-read-experts-opinion https://eventprime.co/o/GoldenFountainFarmsCBDGummiesus https://eventprime.co/o/GoldenFountainFarmsCBDGummiesusa https://www.zupyak.com/p/4646394/t/golden-fountain-farms-cbd-gummies-review-my-honest-opinion-and-results https://www.zupyak.com/p/4646401/t/golden-fountain-farms-cbd-gummies-is-it-safe-read-experts-opinion https://www.zupyak.com/p/4646411/t/golden-fountain-farms-cbd-gummies-review-truth-must-read-before-buying https://www.zupyak.com/p/4646413/t/golden-fountain-farms-cbd-gummies-whats-inside-and-how-it-works https://medium.com/hidyloxi/golden-fountain-farms-cbd-gummies-official-website-must-read-before-buy-f4189ba2b056
https://medium.com/@hidyloxi/golden-fountain-farms-cbd-gummies-is-it-safe-read-experts-opinion-f3c39a3c0b55
https://www.facebook.com/Zyrexin.Para.Que.Sirve
https://www.facebook.com/groups/zyrexinparaquesirve
https://www.facebook.com/events/787231967059840/
https://www.facebook.com/groups/zyrexin.para.que.sirve.2025
https://www.facebook.com/events/1467763294645809/
https://groups.google.com/g/zyrexin-para-que-sirve/c/pNMZP5XVbcw
https://sites.google.com/view/zyrexin-para-que-sirve
https://www.trysmallbiz.com/articles/zyrexin-para-que-sirve-is-it-safe-effective-read-it-before-buy
https://www.trysmallbiz.com/articles/zyrexin-para-que-sirve-review-is-it-really-worth-the-hype
https://www.trysmallbiz.com/articles/zyrexin-para-que-sirve-review-truth-must-read-before-buying
https://www.trysmallbiz.com/articles/zyrexin-para-que-sirve-reviews-cost-scam-exposed
https://zyrexinparaqu.alboompro.com/portfolio/news/1544332-zyrexin-para-que-sirve-is-it-safe-effective-read-it-before-buy
https://zyrexinparaqu.alboompro.com/portfolio/news/1544333-zyrexin-para-que-sirve-review-is-it-really-worth-the-hype
https://zyrexinparaqu.alboompro.com/portfolio/news/1544334-zyrexin-para-que-sirve-review-truth-must-read-before-buying
https://zyrexinparaqu.alboompro.com/portfolio/news/1544335-zyrexin-para-que-sirve-reviews-cost-scam-exposed
https://blog.mycareindia.co.in/zyrexin-para-que-sirve-review-is-it-really-worth-the-hype/
https://blog.mycareindia.co.in/zyrexin-para-que-sirve-can-it-really-improve-your-confidence/
https://blog.mycareindia.co.in/zyrexin-para-que-sirve-reviews-cost-scam-exposed/
https://blog.mycareindia.co.in/zyrexin-para-que-sirve-official-is-it-worth-the-hype/
https://eventprime.co/o/ZyrexinParaQueSirve
https://eventprime.co/o/ZyrexinParaQueSirveusa
https://medium.com/rojelio.doss/zyrexin-para-que-sirve-can-it-really-improve-your-confidence-c8244984db35 https://medium.com/rojelio.doss/zyrexin-para-que-sirve-review-is-it-really-worth-the-hype-4c4424e4f13f
https://www.facebook.com/BrunoMaleEnhancementAustraliaNew2025/
https://www.facebook.com/groups/brunomaleenhancementaustraliaofficial2025
https://www.facebook.com/groups/brunomaleenhancementaustralia.aus
https://www.facebook.com/events/1256498776204967
https://www.facebook.com/events/3349920685173765
https://www.trysmallbiz.com/articles/bruno-male-enhancement-australia-is-it-safe-read-experts-opinion
https://www.trysmallbiz.com/articles/bruno-male-enhancement-australia-reviews-2025-does-it-work
https://www.trysmallbiz.com/articles/bruno-male-enhancement-australia-a-breakthrough-for-male-performance-stamina
https://www.trysmallbiz.com/articles/bruno-male-enhancement-australia-official-website-must-read-before-buy
https://www.facebook.com/OxviaMaleEnhancementGummiesusa/
https://www.facebook.com/groups/oxviamaleenhancementgummiesus
https://www.facebook.com/groups/oxviamaleenhancementgummies2025
https://www.facebook.com/events/1265505828547543
https://www.facebook.com/events/987921380043385
https://www.facebook.com/SerenityVowCBDGummiesUSA/
https://www.facebook.com/groups/serenityvowcbdgummies2025
https://www.facebook.com/groups/serenityvowcbdgummiesusa
https://www.facebook.com/events/767600409086247/
https://www.facebook.com/events/1495170468074781/
Ereforce Male Enhancement: Revitalize Your Performance Naturally
Introduction: Unlock Your Full Potential with Ereforce
In today’s fast-paced and high-stress lifestyle, many men face challenges related to sexual performance, stamina, and overall vitality. Whether due to age, poor diet, or stress, these issues can affect confidence and relationships.
►Visit The Official Website To Get Your Bottle Now◄
https://whoherbs.com/Ereforce
https://www.facebook.com/EreforceMaleEnhancement.Official
https://www.facebook.com/Ereforce.ME.Enhancement
https://www.facebook.com/groups/ereforcemaleenhancement.2025/
https://www.facebook.com/groups/ereforce.male.enhancement.us
https://www.facebook.com/events/737787488975387/
https://www.facebook.com/events/1674286863285964/
https://nas.io/ereforcemaleenhancement/challenges/ereforce-male-enhancement-reviews-does-it-work-or-not
https://nas.io/ereforcemaleenhancement/challenges/ereforce-male-enhancement-mens-health
https://nas.io/ereforcemaleenhancement/challenges/ereforce-male-enhancement-reviews-cost-scam-exposed
https://nas.io/ereforcemaleenhancement/challenges/ereforce-male-enhancement-review-truth-must-read-before-buying
https://eventprime.co/o/ereforcemaleenhancement
https://eventprime.co/o/ereforcemaleenhancementus
https://cbtu.nationbuilder.com/ereforcemaleenhancement2025
https://cbtu.nationbuilder.com/ereforcemeenhancementus
https://paddling.com/paddle/trips/ereforce-male-enhancement-can-it-really-improve-your-confidence
https://paddling.com/paddle/trips/ereforce-male-enhancement-is-it-safe-read-experts-opinion-2
https://paddling.com/paddle/trips/ereforce-male-enhancement-expert-review-is-it-worth-your-money
https://paddling.com/paddle/trips/ereforce-male-enhancementreview-my-honest-opinion-and-results
https://blog.mycareindia.co.in/ereforce-male-enhancement-expert-review-is-it-worth-your-money/
https://blog.mycareindia.co.in/ereforce-male-enhancement-reviews-cost-scam-exposed/
https://blog.mycareindia.co.in/ereforce-male-enhancement-review-is-it-really-worth-the-hype/
https://blog.mycareindia.co.in/ereforce-male-enhancement-official-website-heres-what-experts-say/
https://cbtu.nationbuilder.com/staminoxofficial
https://www.facebook.com/TranquilVibeCBDGummiesbusiness/
https://www.facebook.com/groups/tranquilvibecbdgummiesbusiness2025
https://www.facebook.com/events/1409344806827017/
https://eventprime.co/o/TranquilVibeCBDGummiesUsa
https://eventprime.co/o/TranquilVibeCBDGummiesbusiness
https://paddling.com/paddle/trips/tranquil-vibe-cbd-gummies-official-website-clinical-certified-100-natural
https://paddling.com/paddle/trips/tranquil-vibe-cbd-gummies-expert-review-is-it-worth-your-money
https://www.facebook.com/Staminox.us
https://www.facebook.com/groups/staminox
https://www.facebook.com/events/681142181629757/
https://paddling.com/paddle/trips/tranquil-vibe-cbd-gummies-full-review-benefits-where-to-buy
https://paddling.com/paddle/trips/tranquil-vibe-cbd-gummies-review-2025-truth-behind-the-claims
https://cbtu.nationbuilder.com/tranquilvibecbdgummies
https://blog.mycareindia.co.in/tranquil-vibe-cbd-gummies-official-website-clinical-certified-100-natural/
https://blog.mycareindia.co.in/tranquil-vibe-cbd-gummies-expert-review-is-it-worth-your-money/
https://blog.mycareindia.co.in/tranquil-vibe-cbd-gummies-full-review-benefits-where-to-buy/
https://blog.mycareindia.co.in/tranquil-vibe-cbd-gummies-review-2025-truth-behind-the-claims/
https://www.facebook.com/IronBoosterMaleEnhancementGummiesusa2025/
https://www.facebook.com/groups/ironboostermaleenhancementgummiesofficial2025
https://www.facebook.com/events/1986339115502754
https://nas.io/iron-booster-male-enhancement-gummies-ae56zx/challenges/iron-booster-male-enhancement-gummies-the-fixings-and-advantages-so-compelling
https://nas.io/iron-booster-male-enhancement-gummies-ae56zx/challenges/iron-booster-male-enhancement-gummies-how-does-iron-booster-gummies-work-
https://nas.io/iron-booster-male-enhancement-gummies-ae56zx/challenges/iron-booster-male-enhancement-gummies-allnatural-reviews-1-pack-60-gummies
https://nas.io/iron-booster-male-enhancement-gummies-ae56zx/challenges/iron-booster-male-enhancement-gummies-natural-testosterone-booster-for-men
https://cbtu.nationbuilder.com/ironboostermaleenhancementgummies
https://cbtu.nationbuilder.com/ironboostermaleenhancementgummiesusa
https://paddling.com/paddle/trips/iron-booster-male-enhancement-gummies-natural-reviews-1-pack-60-gummies
https://paddling.com/paddle/trips/iron-booster-male-enhancement-gummies-natural-reviews-5-pack-300-gummies
https://paddling.com/paddle/trips/iron-booster-male-enhancement-gummies-the-fixings-and-advantages-so-compelling
https://paddling.com/paddle/trips/iron-booster-male-enhancement-gummies-what-to-know-about-these-ed-treatments
https://eventprime.co/o/IronBoosterMaleEnhancementGummiesus
https://eventprime.co/o/IronBoosterMaleEnhancementGummiesusa2025
https://blog.mycareindia.co.in/iron-booster-male-enhancement-gummies-natural-testosterone-booster-for-men-2/
https://blog.mycareindia.co.in/iron-booster-male-enhancement-gummies-advanced-powerful-male-enhancement-gummy/
https://blog.mycareindia.co.in/iron-booster-male-enhancement-gummies-what-to-know-about-these-ed-treatments/
https://blog.mycareindia.co.in/iron-booster-male-enhancement-gummies-rely-only-on-proven-methods-2/